What is a Busbar?
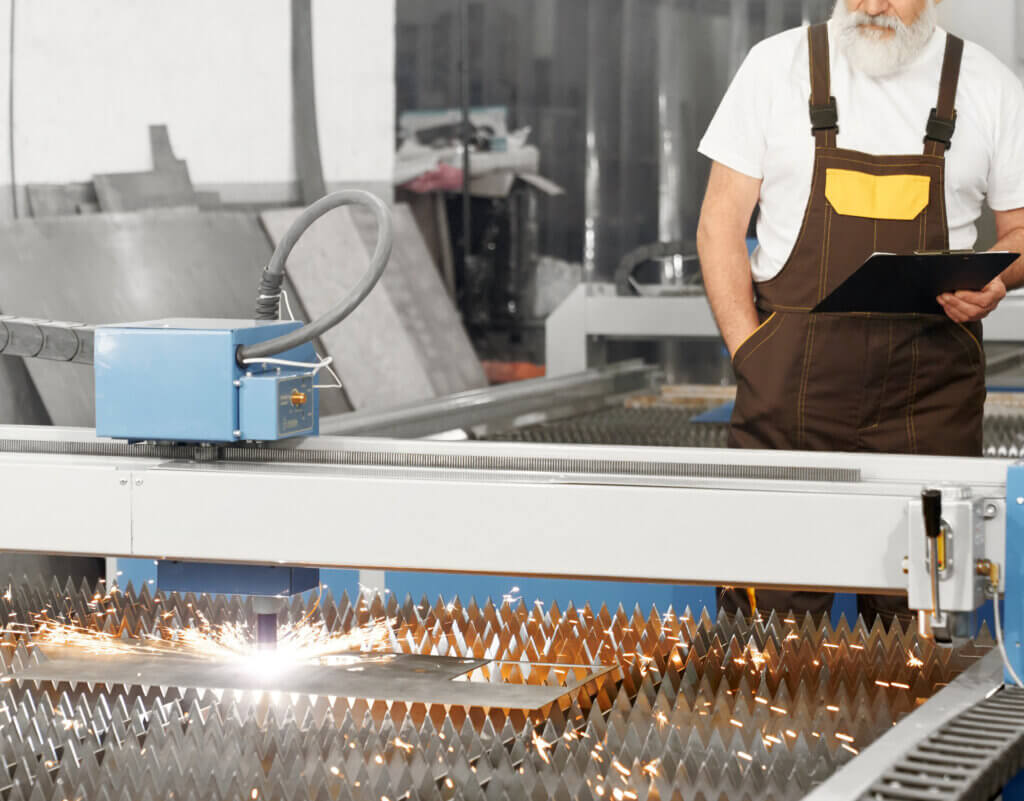
A busbar is a crucial component in electrical power distribution systems, designed to conduct and distribute electric power. Typically made of highly conductive materials like copper or aluminum, busbars are utilized in a variety of industrial, commercial, and residential applications. These systems ensure efficient power transfer and are fundamental in ensuring safe and reliable operations in electrical setups.
Busbars are widely used in power distribution boards, switchgear, transformers, and other equipment. Their primary purpose is to consolidate and distribute large currents, reducing the need for multiple wiring and ensuring seamless connectivity.
Importance of Busbars in Electrical Systems
Busbars play a pivotal role in ensuring efficient, safe, and scalable power distribution within electrical systems. Here are the key benefits:
Efficiency: Busbars provide a streamlined method for distributing electricity, minimizing energy losses, and ensuring maximum efficiency. Their design allows for optimal current flow, reducing resistance and power wastage, which is critical in high-demand applications.
Safety: Proper insulation and installation of busbars significantly lower the risks of electrical faults, short circuits, and other hazards. They are designed to handle high currents safely, making them a reliable choice for electrical infrastructure.
Scalability: Busbars are highly adaptable, with customizable configurations to suit various voltage and current requirements. This flexibility makes them ideal for systems that need to expand or adapt to changing demands.
Compact Design: Unlike traditional wiring methods, busbars offer a more organized and space-saving solution. Their compact layout reduces clutter in electrical panels and enhances accessibility for maintenance and upgrades.
What is CNC Busbar Machinery? And Explain the Features?
CNC Busbar Machinery refers to advanced automated machines designed for manufacturing and processing busbars, which are crucial components in electrical power distribution systems. These machines leverage Computer Numerical Control (CNC) technology to perform precise operations such as cutting, bending, punching, and assembling busbars. By automating these tasks, a CNC busbar machine ensures consistency, efficiency, and accuracy in production, making it essential for industries involved in large-scale electrical infrastructure.
Key Features of CNC Busbar Machinery:
- High Precision: Automated control systems deliver unparalleled accuracy in shaping and processing busbars, reducing material waste and errors.
- Automation: CNC machines minimize manual intervention, significantly boosting productivity while ensuring uniformity in quality.
- Flexibility: These machines can handle different busbar materials (e.g., copper, aluminum) and dimensions, allowing customization for various electrical systems.
- Multi-functionality: Capable of performing several operations—cutting, punching, and bending—on a single platform.
- Energy Efficiency: Modern designs ensure optimized energy use, contributing to cost-effective manufacturing.
By integrating CNC technology, busbar machinery meets the demands of precision-driven industries like power generation, automotive manufacturing, and data centers, ensuring reliability and performance in critical electrical systems.
Types of CNC Busbar Machinery
CNC busbar machinery is essential for processing copper and aluminum busbars, widely used in power distribution systems. These machines enhance precision, efficiency, and versatility in manufacturing busbars. The main types of CNC busbar machinery include:
1. Busbar Cutting Machines
These machines are designed to cut busbars to precise lengths with clean, burr-free edges. Using advanced CNC technology, they minimize material waste and ensure smooth edges, reducing the need for additional finishing processes. They are critical for maintaining the exact dimensions required in high-performance electrical systems.
2. Busbar Punching Machines
Busbar punching machines are used to create holes, slots, or custom shapes in busbars. With programmable CNC controls, they ensure precision and consistency, enabling busbars to fit accurately in electrical connections. These machines often support high-speed operations, improving productivity in industrial applications.
3. Busbar Bending Machines
These machines bend busbars into various angles and shapes while maintaining the material’s structural integrity. CNC controls allow for high accuracy, enabling manufacturers to meet complex design specifications. The ability to program multiple bend angles increases efficiency in producing custom busbars.
4. Busbar Chamfering Machines
Chamfering machines smooth the sharp edges of busbars after cutting, ensuring safe handling and proper electrical insulation. This process also enhances the overall quality of the busbar, making it suitable for applications where safety and precision are critical.
5. Multifunctional Busbar Machines
These machines combine cutting, punching, and bending functions into one compact unit, offering an all-in-one solution for busbar processing. They are ideal for manufacturers with limited space or those requiring high flexibility and efficiency.
6. Busbar Insulation Machines
Insulation machines apply a protective coating or layer to busbars, enhancing their resistance to electrical shorts and corrosion. They are crucial in applications where busbars are exposed to harsh environments.
7. Busbar Assembly Machines
These specialized machines are used for assembling busbars into larger systems, such as bus ducts or busways. They ensure precise alignment and fastening of components, streamlining the production process.
CNC busbar machinery is indispensable for modern manufacturing, enabling precise, efficient, and high-quality processing of busbars to meet the diverse needs of electrical power systems. These machines reduce labor costs, improve productivity, and ensure compliance with industry standards.
What is CNC Busway Machinery? Explain the Benefits of Busway Machines?
CNC Busway Machinery refers to automated equipment designed to process busbars or busways, which are essential components in power distribution systems. These machines use Computer Numerical Control (CNC) technology to perform precise operations such as cutting, punching, bending, and chamfering on copper and aluminum busbars. CNC Busway Machinery plays a crucial role in manufacturing high-quality busways, ensuring reliability and efficiency in power distribution.
Benefits of CNC Busway Machinery
- Precision and Accuracy: CNC technology ensures exact specifications, reducing errors and material waste.
- Increased Productivity: Automated operations enable faster production rates compared to manual processes.
- Cost-Effectiveness: Reduces labor costs while minimizing material wastage through optimized processes.
- Versatility: Suitable for various busbar materials and sizes, catering to diverse power distribution requirements.
- Safety: Advanced features and automation reduce the risk of accidents and ensure consistent quality.
Comparison of CNC Busbar and Busway Machines
Feature | CNC Busbar Machines | Busway Machines |
Primary Use | Cutting, bending, punching busbars | Manufacturing busway systems |
Automation Level | High | High |
Key Operations | Multi-functional processing | Assembly and insulation |
Applications | Electrical panels, transformers | Modular power distribution |
Scalability | Highly customizable | Easily extendable systems |
Future of CNC Busbar and Busway Machinery
As power distribution requirements continue to evolve with the rise of renewable energy, electric vehicles, and smart grids, the demand for advanced busbar and busway systems will grow. CNC technology will continue to play a pivotal role in optimizing the production processes, improving the efficiency, and expanding the capabilities of busbar and busway systems. Future developments in CNC machinery may include:
- Integration with IoT: Incorporating sensors and connectivity into CNC machines to allow real-time monitoring and predictive maintenance.
- Advanced Materials: Development of CNC machines capable of handling new materials for busbars and busways, such as composite materials or superconducting materials.
- Automation: Increased use of robotics and AI to fully automate busbar and busway production, reducing human involvement and further enhancing precision and speed.
Conclusion
Busbars are indispensable components in modern electrical systems, offering efficient and reliable power distribution. CNC busbar and busway machinery have revolutionized the manufacturing processes, ensuring precision, scalability, and cost-effectiveness. From cutting and bending to assembly and testing, these machines cater to the diverse needs of industries worldwide.
Investing in high-quality CNC busbar and busway machinery ensures superior performance, reduced operational costs, and long-term reliability. Whether you are a small-scale manufacturer or a large industrial player, understanding and leveraging these technologies will help you stay ahead in the competitive electrical manufacturing industry.