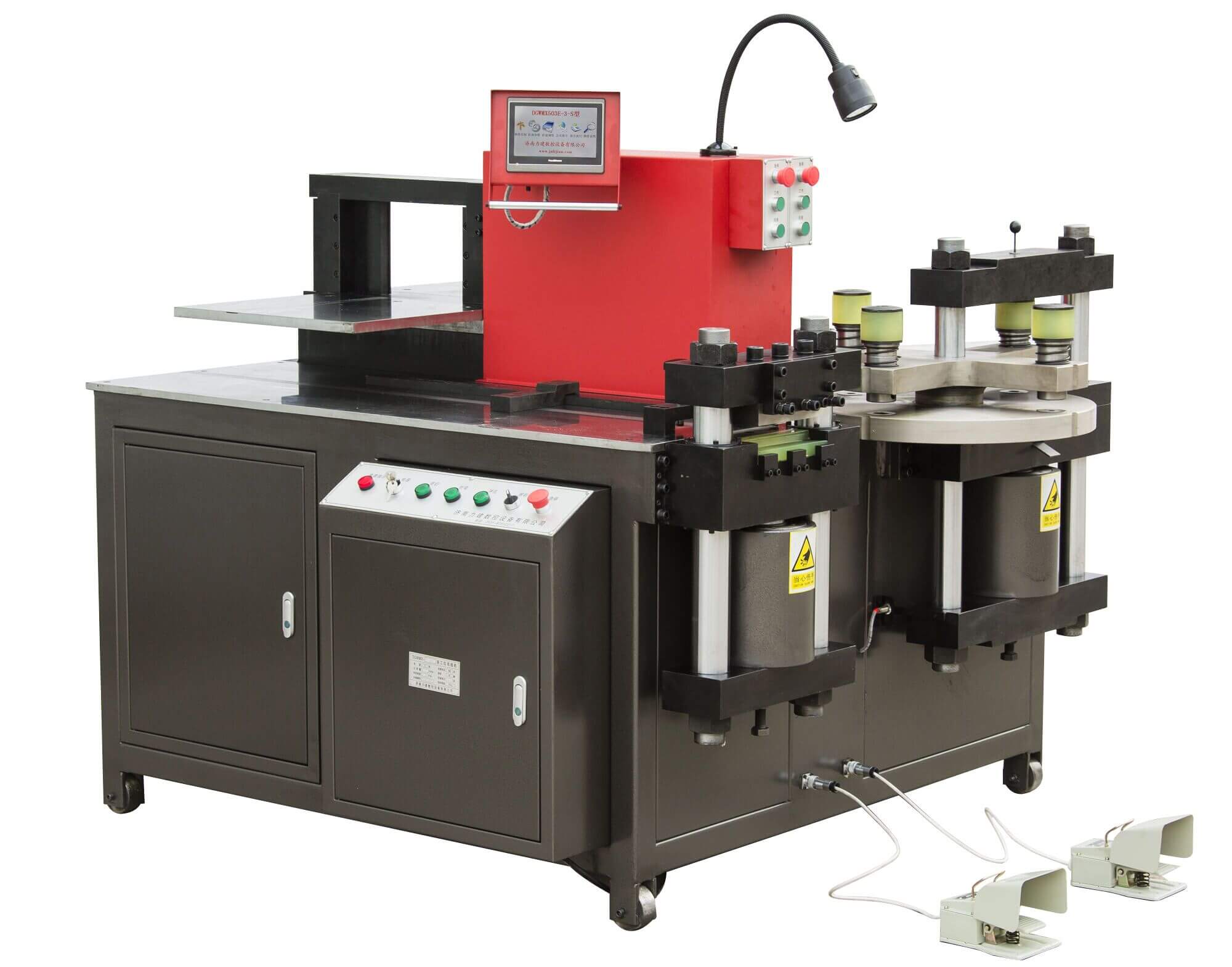
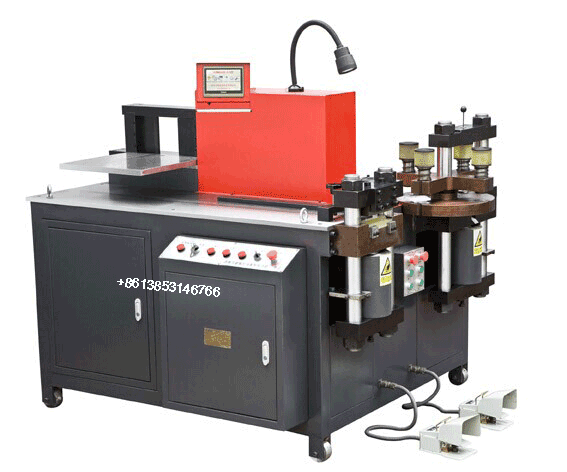
503E-3-S Hydraulic Busbar Bending Punching Cutting Machine in India
Price 8,3000$-19,000$. (According to different axe, power, and parts… prices are much different)
The hydraulic busbar machine is mainly used for various specifications of copper, and aluminum busbar processing. The hydraulic busbar machine can respectively or simultaneously punch, shear, bend processing, simple operation, convenient use, and high production efficiency, is specially used for the power industry, high and low voltage complete sets, and busbar industry processing copper and aluminum busbar special equipment.
The 503E-3-S Hydraulic Busbar Bending Punching Cutting Machine offers high efficiency and precision for busbar processing. Designed for durability and performance, it ensures seamless bending, punching, and cutting operations. Get the best Hydraulic Busbar Bending Punching Cutting Machine in India for superior productivity!
Main Functions of 503E-3-S Hydraulic Busbar Machine
Cutting, punching, bending (vertical bending, flat bending, u bending, offset bending), twisting chamfering, embossing (various circular holes, square holes, special-shaped holes, and groove shapes), and other processing of copper and aluminum busbars.
Simple operation, convenient use, and high production efficiency are specially used for the power industry, high and low voltage complete sets, and busbar industry processing copper and aluminum busbar special equipment.
The Main Features of Hydraulic Busbar Bending Cutting Punching Machine:
✅The machine has three processing units of punching, cutting, and bending, which can respectively carry out the punching, cutting, and bending processing of the bus bar. You can also choose the special processing of flattening, embossing, pressing cable joints, buttons, and so on.
✅The machine adopts the double-layer workbench design scheme, three stations can work at the same time without affecting each other, is easy to use, and production efficiency is higher than the traditional busbar processing equipment.
✅The working stroke of each unit can be conveniently adjusted to reduce processing auxiliary time and improve production efficiency.
✅Punching and shearing unit with vertical processing, flexible and convenient operation, shear using flat shear or punching shear, shear workpiece flat.
✅The bending unit is horizontal, and the bending of flat and vertical bending can be achieved by replacing the mold. The bending unit of the CNC busbar processing machine adopts numerical control mode and has a memory function.
✅Through the replacement of the mold can also achieve a variety of processing functions, such as embossing, flattening, pressing cable joints and button twists, etc.
✅The punching unit of the turret busbar processing machine adopts the turret structure, which can assemble 4/6/8 sets of punching dies at one time. Can choose the appropriate punching mold to work, a simple operation.
Main Features of our dgwmx503E-3-S:
- The cutting unit adopts a double-column shear structure (patent number: ZL201120262802.1), Cut mouth flat, no burr, and no waste.
- The punching unit adopts Nodular cast iron,4/6/8 modes position turret punching structure which is a total whole one, improving the concentric degree of molds, prolonging the service life of the molds, and saving time for a change.
- The bending unit adopts a closed bending structure, making it more uniform when processing horizontal bending and embossing. Also prolonging the service life.
- The bending unit adopts a double work table, achieving a real sense of the three positions working at the same time while working without impacting each other.
- Adopting PLC controlled, the bending angle can be CNC controlled and with a storage function.
- Three units of the machine can work at the same time, not affecting each other, Improving the processing efficiency.
- Hydraulic tank with thick plate welding, and is treated by phosphating, making hydraulic oil can be long time used and will not degenerate.
Bidirectional positioning:
The perfect combination of bidirectional positioning design of the punching station and table scale makes the busbar punch more accurate, improves work efficiency, and reduces the generation of defective products.

Imported Siemens PLC:
Adopt imported Siemens PLC to ensure the safety and stability of the circuit.
Avoid machine failure, more durable.
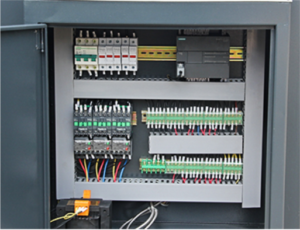
Strong driving force:
Three power motors are used.
Ensure the dynamic stability of the three stations and that each of them does not interfere with the other.
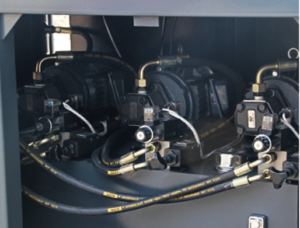
Touch control screen:
The touch control screen, and intelligent control system accurately set parameters to achieve intelligent control.
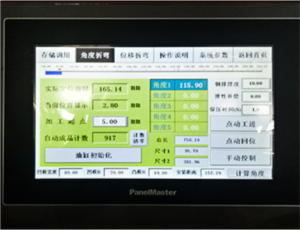
Hydraulic tank special treatment:
The 3mm thick steel plate is welded and treated with phosphating to prevent pollution and corrosion of hydraulic oil.
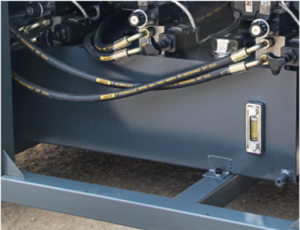
DGWMX503E-3-S hydraulic busbar machine
型号 Item |
DGWMX503E-3 |
DGWMX503E-3-S |
公称压力 Nominal pressure |
500KN |
500KN |
最大加工尺寸 Max. processing size |
16×200mm |
16×200mm |
冲孔加工范围 Punching diameter range |
Φ4.3-32mm |
Φ4.3-32mm |
最大立弯折弯宽度 Max. vertical bending width |
120mm |
120mm |
工作台尺寸 Work bench size |
一层台First worktable:1600mm×1400mm 二层台Second worktable:1020mm×500mm |
一层台First worktable:1600mm×1400mm 二层台Second worktable:1020mm×500mm |
设备尺寸 Size of the machine |
1920mm×1550mm×1500mm |
1920mm×1550mm×1500mm |
设备重量 Weight of the machine |
1870kg |
1900kg |
折弯角度数控 Bending angle cnc |
否NO |
是YES |
三工位同时工作 The three units work at the same time |
是YES |
是YES |
Main parts:



